High Carbon Silicon| New Solution for Steelmaking Deoxidation
Introduction
High carbon silicon is a new composite deoxidizer with great content of silicon and carbon, also known as silicon-carbon alloy. It is mainly used in the steelmaking and foundry industry. Compare with traditional materials, ferrosilicon, for example, high carbon silicon has a faster reaction with oxygen in the process of deoxidation.
Production
High carbon silicon is the by-product of silicon metal. It is together with silicon slag that is in the bottom of furnace. Normally, the silicon content will reach 65% to 68%, grades Si65C18 and Si68C18 are the most popular.
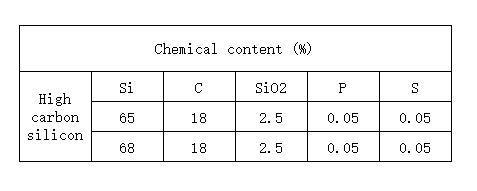
Advantages
1. High carbon silicon is beneficial for the furnace temperature. The chemical reaction of silicon and oxygen produces SiO2, which also releases large amount of heat. Therefore, high-carbon silicon can replace the traditional heating agent with a higher price in converter and hearth furnace steelmaking. Its application helps to reduce the production cost, faster deoxidation saves electricity bills.
2. Improved alloy recovery (alloying in the ladle). The recovery rate has increased from about 8% to about 50%. The recovery rate of high carbon silicon can be increased by about 2% after being used with ferromanganese and ferrosilicon.
3. Reduce the usage of aluminum. The amount of high carbon silicon is added in the amount of one kilogram per ton of steel. The consumption of aluminum is reduced from 1kg/T steel to 0.3kg/T steel; calcium silicon is no longer used, and the consumption of ferrosilicon and ferromanganese can be reduced from the usual amount.
Market
As the cost of electricity continues to rise, the actual economic benefits of high carbon silicon are far greater than the calculations on paper, and there are significant social benefits.
.jpg)
For further information please get in touch with Hainan West Asia Group Co. LTD